Vibrating Fork Level Sensor Principle and Comparison
By Dhananjay Palshikar on April 18, 2019
BeginnerIntroduction
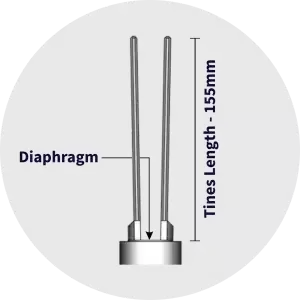
History: Tuning Fork Level Sensor
Tuning fork level switches have been commonly used in the industry since the 1970s. They were introduced as alternatives to Rotating Paddle Level Switches. Vibrating Fork Level Sensors have stood the test of time and continue to dominate the point level switch market.
Sapcon Instruments has been manufacturing vibrating fork level sensors since its inception in the year 1983. Sapcon contributed over 35+ years as one of the best vibrating fork type level switch manufacturer in India. Since then, Vibrating fork has evolved into a compact and fast level switch. The success and popularity of these level sensors can largely be attributed to:
- Calibration Free Operation
- Relatively Long Operational Life Expectancy
How do the tuning fork tines vibrate?
Pressure applied by the piezoelectric stack on the diaphragm causes it to shear, which in turn drives the tuning fork's tines apart from each other. See the figure given aside for a simulation of the process. When the pressure is removed the fork tines return to their original position.
The application of force when applied at the fork's Natural Frequency makes it oscillate at its maximum amplitude for a given power.
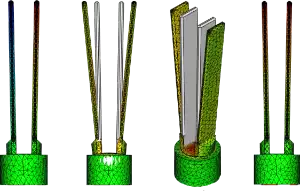
Fork Sensor Working Principle
The working principle of vibrating fork level sensor is based on vibrating a tuning fork sensor continuously at its natural frequency and detecting the change of frequency and amplitude in the presence of application media. The monitoring process of given parameters depends upon type of application media.
- Amplitude of vibration
- Frequency of operation
- Amplitude of vibration: Vibrating Level Switch for Solids
- Frequency of operation: Liquid Level Sensor
As the material level increases and comes in contact with the Vibrating Fork tines, the amplitude of oscillation of tuning fork level switch dampens. When the amplitude goes below a set threshold, the onboard electronics causes a change to the outputs(Relays/ PNP).
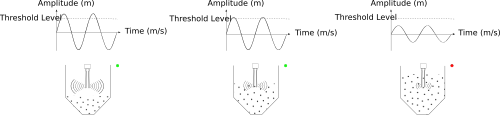
The natural frequency of oscillation for the tuning fork level switch decreases as it covered with the liquid application media. The threshold frequency is set to match the natural frequency of tuning fork type level switch under water as shown here:
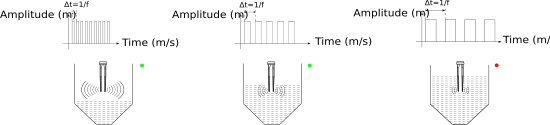
Switching Point Hysteresis for Point Level Switching
Turbulence can be caused by flow of material or due to an agitator or stirrer inside the silos. This can cause fluctuations in both the amplitude and frequency of operation for the tuning fork. For reliable level sensing a switching hysteresis is maintained around the swiching point.
This prevents frequent toggling around the switching point. In vibrating fork for solids, changing the sensitivity may affect the hysteresis for the sensor. In general hysteresis margin decreases with increase in sensitivity. The natural frequency of tuning fork increases with increase in the length of tines.
A comparison of the tuning forks vis-a-vis their performance and end-use has been shown below for a better understanding.
Tines Length | 220mm | 155mm | Vital-100mm | Elixir-100mm | 44mm |
---|---|---|---|---|---|
Application Media | Solids | Solids | Solids | Liquids/Solids | Liquids |
Natural Frequency in air (Hz) approx. | 80 | 150 | 300 | 300 | 1600 |
Buildup Immunity |
|
||||
Response Time (Fastest) | 3 sec | 2 sec | 0.5 sec | 1 sec | 1 sec |
Typical Application | General Purpose | General Purpose | Fast packaging machines & compact silos | Non-foaming liquids or free-flowing Solids | Hygienic Design. free-flowing liquids, liquids with foam, compact silos |
Products
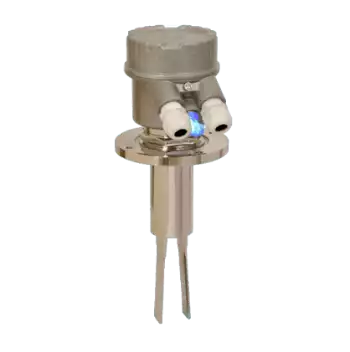
Vital
Vibrating Fork Level Sensor
Vibrating level switch for free-flowing solids, granules and powders.
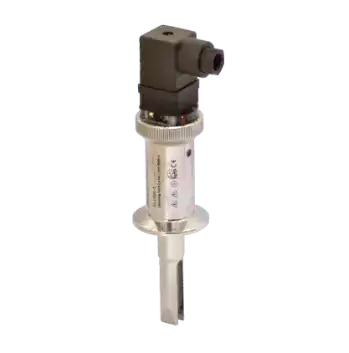
Elixir-T-Uni
Tuning Fork Level Sensor
Compact tubular vibrating fork type sensor suitable for all kinds of liquids.
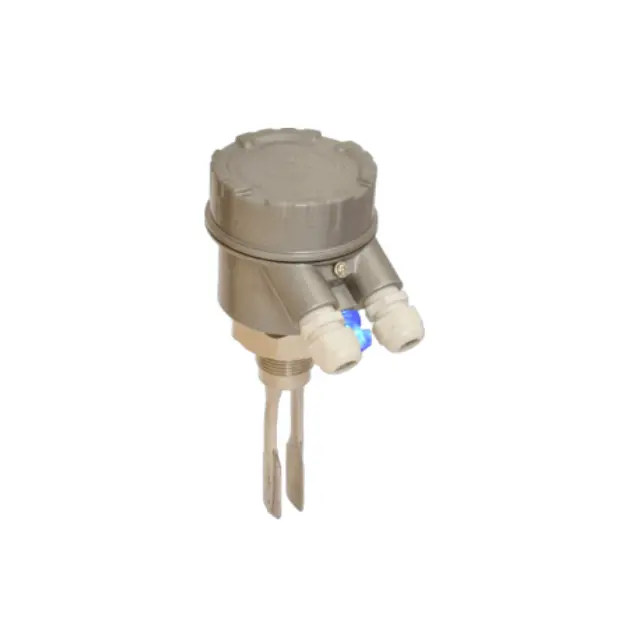
Elixir
Tuning Fork Level Sensor
Vibrating Fork type Level Switch suitable for storage tanks, mixing containers etc.
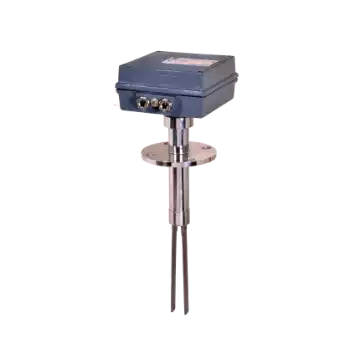
SLM
Vibrating Fork Level Sensor
Vibrating Fork Level Switch for free-flowing Solids, Granules and Powders.
Vibrating Level Switch It has various outputs such as: NAMUR, IO-LINK, RELAY and transistor Adaksepehr