Moisture Separator
By Megha Parolkar on May 25, 2019
BeginnerIntroduction
Industrial sectors involve numerous processes and operations that require the intervention of steam operated equipment. However, the most common concern while working with such equipments is when moisture mixes with steam causes problems such as corrosion and water hammer effect and damage costly equipment like flow meters, control valve etc. by deteriorating the internal components. Therefore the presence of moisture in air is unavoidable and also it adversely affects the overall efficiency and performance of the steam operated equipment.
Due to its detrimental effects it becomes neccesary to separate moisture from air that may present in the form of water droplets to rectify dry air and use steam with maximum dryness. For this a Moisture Separator also known as steam separator becomes essential. It is used to separate the water particles from the steam. It play vital role in improving efficiency and quality of overall performance of the steam operated machines.
Operation
- The wet steam entered to the separation unit consist of various baffle plates through inlet valve and it strikes baffle plate causes change in directional flow.
- Due to large cross-sectional area, steam experience a sudden enlargement of volume which reduces the drop in velocity.
- Therefore, the heavier water particles get deposited on baffle plates and steam flows around the baffle.
- When the steam impinges on the baffles inside the separator body water particles are separated from the steam flow-path due to change in the momentum.
- The water is collected at the bottom of the separator and can be drained off through the trap assembly fitted at the bottom of the separator after measuring the water level through level sensor.
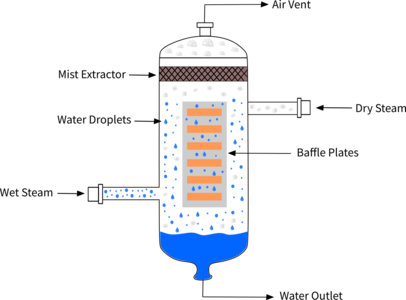
Problem
For the efficient functioning of the system the collected water at the bottom of the separator needs to be drained regularly, if not, there is a likelihood of the excess water particles re-entering the steam flow.
Solution
Instead of depending on manual draining of the condensate water from the collection chamber the draining can be automated by installing an appropriate level sensor from a wide range of level sensors manufactured by Sapcon. It recommended to use Vibrating Fork type liquid level switch “ELIXIR” for such applications. This sensor can be side mounted in the water chamber as a high level detector and the switched output can be used to control solenoid valves to drain the water from the chamber effectively.
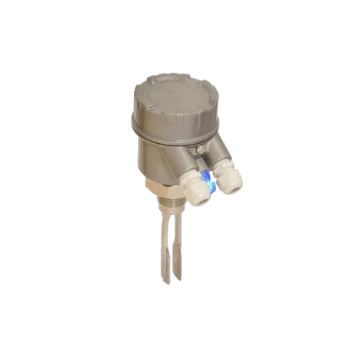
Elixir
Vibrating Fork Level Sensor
Vibrating Fork Liquid Level Switch suitable for level detection in storage tanks, mixing containers etc.
“ELIXIR” Fork tines are made of stainless steel to avoid corrosion. Vibration systems are unaffected by electrical parameters such conductivity and dielectric constant of the service material. The instrument is compact so fits into restricted spaces. It is accurate and has a fast response time; So it is an ideal choice for this application.
More articles on Intro Level Sensor